cable tray sizes
In the realm of electrical installations, the significance of selecting the appropriate cable tray sizes cannot be overstated. These sizes play a pivotal role in ensuring the safety, efficiency, and longevity of your electrical systems. Whether you’re navigating the complexities of 4 SS cable tray sizes, cable tray round sizes, or other specifications, understanding the different sizes and their applications is key. The choice of the correct cable tray size can significantly impact not only the current functionality of your systems but also their future scalability and maintenance. Let’s delve deeper into the intricacies and considerations involved in choosing cable tray sizes.
Understanding Cable Tray Systems
Before we delve into specific sizes, it’s crucial to grasp the role of cable trays in managing cables and why they are indispensable. Cable trays serve as a vital component in electrical and telecommunication infrastructure, offering an organized and practical solution for routing cables. They are especially crucial in large-scale facilities where the volume of cables can be overwhelming. The design of cable trays allows for the secure placement of cables while keeping them accessible for necessary maintenance or future upgrades.
What Are Cable Trays?
Cable trays are support systems used to manage cables in various settings, including commercial buildings, industrial facilities, and data centers. They provide a secure and organized pathway for electrical and data cables, ensuring they are protected and easily accessible. These structures can vary in material, type, and size, depending on the specific needs of the installation environment.
Why Use Cable Trays?
The primary reason for using cable trays is to ensure a neat and organized cable management system. Without cable trays, cables can become tangled, leading to potential hazards and difficulties in troubleshooting. Cable trays also offer protection to cables against physical damage and environmental factors. By elevating the cables, they reduce the risk of exposure to harmful elements and mitigate the chances of mechanical damage.
Benefits of Cable Trays
Cable trays offer a host of advantages over traditional conduit systems, making them a superior choice for cable management. They provide easier installation and access for maintenance or upgrades, which can significantly reduce labor costs. Cable trays also allow for better airflow around the cables, preventing overheating and extending the lifespan of the cables. Furthermore, they offer flexibility in design, accommodating future expansions or modifications without significant disruptions.
Types of Cable Trays
There are several types of cable trays available, each designed for specific applications. Understanding the differences between these types can help in selecting the right one for your specific requirements. The most common types include:
1. Ladder Cable Trays
Ladder cable trays are one of the most popular types used in industrial settings. They consist of two side rails with rungs in between, resembling a ladder. This design allows for excellent ventilation and easy cable installation, which is crucial in environments with high heat generation.
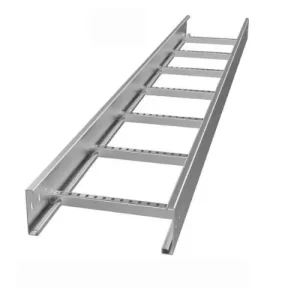
Advantages of Ladder Cable Trays
The open design of ladder cable trays facilitates easy installation and maintenance. The rungs provide ample space for cable tie-downs, ensuring the cables remain securely in place. The ventilation offered by this design helps in dissipating heat and protecting cables from thermal damage.
Applications of Ladder Cable Trays
These trays are ideal for environments where airflow around the cables is essential. They are commonly used in industrial facilities and factories where machinery generates significant heat. The robust construction of ladder trays makes them suitable for supporting heavy cable bundles.
Materials Used in Ladder Cable Trays
Ladder trays can be made from various materials, including aluminum, steel, and fiberglass. The choice of material often depends on environmental conditions and the need for corrosion resistance or lightweight construction.
2. Perforated Cable Trays
Perforated cable trays feature a solid bottom with holes, providing ventilation and heat dissipation for the cables. They are ideal for environments where dust accumulation is a concern, as the perforations allow for easy cleaning and maintenance.
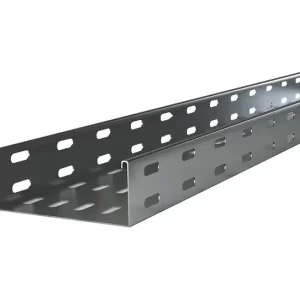
Benefits of Perforated Cable Trays
The perforations not only aid in ventilation but also reduce the overall weight of the tray, making it easier to handle during installation. These trays offer a balance between solid bottom trays and ladder trays, protecting while still allowing for airflow.
Common Uses for Perforated Trays
Perforated trays are suitable for indoor installations where dust is a concern. They are often used in commercial buildings and offices where aesthetics and functionality need to be balanced. These trays are also ideal in environments with moderate heat generation.
Material Choices for Perforated Trays
These trays are typically made from materials like galvanized steel, stainless steel, or aluminum, offering varying levels of corrosion resistance and strength. The choice of material will depend on the specific environmental conditions and budget considerations.
3. Solid Bottom Cable Trays
Solid bottom trays have a continuous, flat surface without any perforations. They offer maximum protection for cables against external factors like dust and moisture, making them suitable for sensitive environments where cable integrity is paramount.
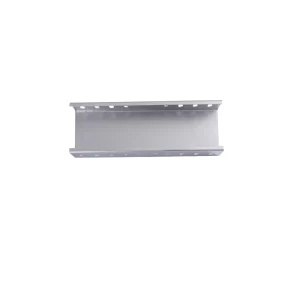
Protection Offered by Solid Bottom Trays
The solid design provides a shield against environmental contaminants, which is particularly important in cleanroom environments or areas with high levels of dust. This protection helps in maintaining the integrity and performance of sensitive cables.
Where to Use Solid Bottom Trays
These trays are ideal for environments that require a high level of cleanliness or where cables are exposed to potentially damaging conditions. They are commonly used in pharmaceutical manufacturing, food processing plants, and other cleanroom settings.
Material Considerations for Solid Bottom Trays
Solid bottom trays are often made from materials that offer high corrosion resistance, such as stainless steel or coated steel. The material choice ensures longevity and reliability, even in harsh conditions.
4. Wire Mesh Cable Trays
Wire mesh trays, also known as basket trays, are made of interlocking wires. They are lightweight and flexible, making them perfect for complex cable routing in data centers and communication facilities where adaptability is key.
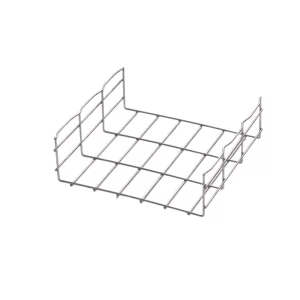
Advantages of Wire Mesh Trays
The flexibility of wire mesh trays allows for quick and easy adjustments to the cable layout, accommodating changes in the network infrastructure. Their lightweight nature makes them easy to install and reposition as needed.
Ideal Environments for Wire Mesh Trays
These trays excel in environments where frequent changes or upgrades to the cable network are expected. Data centers, IT facilities, and telecommunication hubs often utilize wire mesh trays for their ease of use and adaptability.
Material and Construction of Wire Mesh Trays
Wire mesh trays are typically constructed from steel wires that are either galvanized or coated to prevent corrosion. The open design not only allows for excellent ventilation but also enables easy visual inspection of the cables.
Key Factors in Choosing Cable Tray Sizes
When selecting cable tray sizes, several factors need to be considered to ensure optimal performance. The right size will depend on the specific requirements of the installation environment, as well as future scalability considerations.
1. Cable Volume and Type
The size of the cable tray should accommodate the total volume of cables you plan to install. Consider both the number and the diameter of the cables, as well as any future expansion needs. It’s crucial to allow for additional space to prevent overcrowding and ensure proper cable management.
Assessing Cable Volume
Begin by calculating the total number of cables and their respective diameters. This will give you a baseline for the minimum tray size required. Consider future expansions, as adding more cables later may require a larger tray than initially anticipated.
Types of Cables to Consider
Different types of cables, such as power, data, or communication cables, may require specific tray sizes due to their varying diameters and insulation needs. Understanding the specific requirements of each cable type will help in selecting the appropriate tray size.
Planning for Future Needs
Future-proofing your installation by choosing a slightly larger tray size can save time and costs associated with upgrades. Consider potential technological advancements or organizational growth that may necessitate additional cables.
2. Load Capacity
Cable trays must support the weight of the cables without bending or sagging. Check the load capacity of the tray and ensure it meets your requirements. The load capacity will depend on the material and construction of the tray.
Understanding Load Ratings
Manufacturers provide load ratings based on the material and design of the tray. Ensure that the selected tray can handle the expected load, including any additional weight from future cable installations.
Importance of Proper Load Distribution
Proper load distribution is essential to prevent tray deformation or failure. Ensure that the weight of the cables is evenly distributed across the tray to avoid localized stress points.
Selecting a Tray with Adequate Capacity
Consider both the static and dynamic loads that the tray will experience. Static loads include the weight of the cables, while dynamic loads may involve external forces such as vibrations or impacts.
3. Environmental Conditions
Consider the environmental conditions where the cable tray will be installed. For instance, if the tray is exposed to corrosive elements, opt for materials like stainless steel (SS) or galvanized iron (GI) that offer resistance to corrosion.
Analyzing Environmental Impact
Evaluate the installation environment for factors such as humidity, chemical exposure, temperature fluctuations, and physical impacts. Each of these can affect the choice of tray material and size.
Material Selection Based on Environment
Different materials offer varying levels of resistance to environmental conditions. Stainless steel is ideal for corrosive environments, while aluminum may be preferred for areas requiring lightweight construction.
Protective Coatings and Finishes
In environments with extreme conditions, consider trays with protective coatings or special finishes that enhance their durability and resistance to environmental stressors.
4. Installation Space
The available space for installation can also influence the choice of cable tray sizes. Measure the area where the tray will be mounted to ensure a proper fit. Space constraints can limit the size and type of tray that can be used.
Measuring Installation Areas
Accurate measurements of the installation space are crucial for selecting the right tray size. Consider factors such as ceiling height, available wall space, and any obstructions that may affect tray placement.
Adapting to Space Limitations
In areas with limited space, consider using trays with a smaller footprint or those that can be mounted vertically or horizontally to maximize available space.
Customizing Tray Layouts
Custom tray layouts can be designed to fit unique spaces or specific routing requirements. This flexibility allows for optimized cable management even in challenging environments.
Common Cable Tray Sizes
Here are some standard sizes for different types of cable trays. Understanding these standard dimensions can help in planning and installation, ensuring that the trays meet the specific needs of your project.
4 SS Cable Tray Sizes
Stainless steel cable trays are known for their corrosion resistance and durability. Common sizes include:
- Width: 100mm, 150mm, 200mm
- Height: 50mm, 75mm, 100mm
Benefits of Stainless Steel Trays
Stainless steel trays offer unparalleled durability and resistance to corrosion, making them suitable for harsh environments. They are ideal for outdoor installations or areas with high levels of moisture or chemicals.
Standard Widths and Heights
The standard widths and heights cater to various cable volumes and installation requirements. Choosing the right size depends on the specific needs of the project and the environment.
Applications for Stainless Steel Trays
These trays are often used in marine environments, food processing facilities, and chemical plants where corrosion resistance is a priority.
Cable Tray Round Sizes
Round cable trays are often used for specific applications. Typical sizes are:
- Diameter: 100mm, 150mm, 200mm
Unique Features of Round Trays
Round trays provide a distinctive design that can be beneficial in certain routing applications. Their shape can facilitate smoother cable pulls and reduce the risk of cable damage.
Selecting Diameter Based on Application
The diameter of round trays should be chosen based on the volume and type of cables to be housed. Larger diameters are suitable for higher cable volumes or thicker cables.
Specialized Uses for Round Trays
These trays are often employed in telecommunications and data centers where cable routing needs are complex and dynamic.
Cable Laying Work Tray Sizes
For general cable laying work, the tray sizes often vary based on the project requirements. Standard sizes include:
- Width: 100mm, 150mm, 200mm, 300mm
- Height: 50mm, 75mm, 100mm
Versatility in Tray Dimensions
The variety of widths and heights available for cable laying work allows for flexibility in meeting different project specifications and cable volumes.
Choosing the Right Size for the Job
Selecting the right size involves assessing the number and type of cables, as well as the installation environment. Proper sizing ensures efficient cable management and minimizes the need for future adjustments.
Common Applications for Laying Work Trays
These trays are used across a wide range of industries, including construction, manufacturing, and utilities, providing reliable support for extensive cable networks.
Cable Tray GI Sizes
Galvanized iron trays are favored for their strength and affordability. Common sizes are:
- Width: 100mm, 200mm, 300mm, 400mm
- Height: 50mm, 75mm, 100mm
Advantages of Galvanized Iron Trays
GI trays offer a cost-effective solution with excellent strength and durability. The galvanization process provides a protective coating that resists rust and corrosion.
Standard Sizing for GI Trays
The available sizes for GI trays accommodate a range of cable volumes and installation needs, from small-scale projects to large industrial setups.
Typical Uses for GI Trays
These trays are often used in industrial and commercial settings where cost-effectiveness and robust performance are required.
Cable Tray Sizes 100mm
The 100mm width is a versatile choice used across various applications. It is often paired with different heights, such as 50mm or 75mm, to suit specific needs.
Flexibility of 100mm Trays
The 100mm width offers a balance between capacity and space efficiency, making it suitable for diverse applications, from residential to industrial.
Pairing Width with Height
Combining the 100mm width with various heights allows for customization based on the volume and type of cables, as well as the installation environment.
Applications for 100mm Trays
These trays are commonly used in office buildings, retail spaces, and small industrial facilities where space is limited, but cable management is essential.
Installation Tips for Cable Trays
Proper installation of cable trays is vital for ensuring safety and functionality. Here are some tips to keep in mind to optimize the installation process and ensure a reliable cable management system.
Planning the Layout
Before installation, plan the tray layout to ensure efficient cable routing and accessibility. A well-thought-out layout can prevent complications during installation and facilitate future maintenance or upgrades.
Analyzing the Installation Environment
Consider the physical layout of the installation space, including obstacles, access points, and potential hazards. This analysis will help in designing a layout that maximizes efficiency and minimizes risks.
Mapping Cable Routes
Map out the cable routes in advance, considering factors like cable types, lengths, and connection points. This step ensures that cables are routed logically and efficiently, reducing the risk of interference or damage.
Utilizing Design Software
Using design software can aid in visualizing the layout and identifying potential issues before installation. This tool can enhance planning accuracy and streamline the installation process.
Support Spacing
Follow manufacturer guidelines for support spacing to prevent sagging and ensure stability. Proper support spacing is crucial for maintaining the integrity and performance of the cable tray system.
Determining Appropriate Support Intervals
The appropriate support spacing depends on the tray type, material, and load capacity. Adhering to manufacturer recommendations ensures that the trays remain stable and secure.
Installing Supports Correctly
Ensure that supports are installed level and securely fastened to the structure. This stability prevents movement or sagging, which can compromise the cable system.
Adjusting for Environmental Factors
Consider environmental factors, such as temperature fluctuations or vibrations that may affect support spacing. Adjust support intervals accordingly to maintain tray stability under varying conditions.
Securing Connections
Use appropriate hardware to secure tray sections and joints, maintaining structural integrity. Properly secured connections are essential for preventing tray movement and ensuring a reliable cable management system.
Selecting the Right Hardware
Choose hardware that is compatible with the tray material and suitable for the installation environment. The right hardware ensures secure connections and long-term reliability.
Ensuring Tight and Secure Joints
Check that all joints and connections are tightened to prevent any movement or separation. Loose connections can compromise the entire system, leading to potential damage or failure.
Regularly Inspecting Connections
Periodically inspect connections to ensure they remain secure over time. Regular maintenance can catch any potential issues early, preventing larger problems down the line.
Allowing for Expansion
Leave room for future cable additions to avoid overloading the tray. Planning for expansion ensures that the cable management system remains effective as your needs grow.
Designing for Future Growth
Consider potential future requirements when designing the cable tray system. Allowing for extra capacity can reduce the need for costly upgrades or modifications later.
Assessing Current and Future Needs
Evaluate both current cable needs and potential future expansions. This assessment helps in determining the appropriate tray size and layout for long-term effectiveness.
Implementing Flexible Solutions
Incorporate flexible solutions, such as adjustable trays or modular components, to accommodate future changes with minimal disruption. These solutions enable easy adaptation to evolving requirements.
Conclusion
Selecting the right cable tray sizes is essential for maintaining an organized and efficient cable management system. By considering factors like cable volume, load capacity, and environmental conditions, you can choose the best tray sizes for your needs. Whether you’re dealing with 4 SS cable tray sizes or cable tray GI sizes, understanding the options available will help you make informed decisions for your electrical installations.
With the right cable tray system in place, you can ensure the safety and reliability of your electrical infrastructure, supporting your operations for years to come. A well-designed cable management system not only enhances safety and efficiency but also contributes to the overall longevity and performance of your electrical installations. By investing in the right cable tray solutions, you are taking a proactive step towards a more organized and future-proof infrastructure.