Industrial cable trays are an essential component of modern electrical infrastructure, providing a structured and organized means of managing power cables, control cables, and communication cables in industrial facilities. Proper installation of these cable trays is crucial for ensuring the safety, efficiency, and longevity of electrical systems. In this comprehensive article, we will delve deeper into the reasons why proper installation is vital for industrial cable trays and explore the various aspects that contribute to a successful installation process.
1. Electrical Safety and Proper Installation
One of the primary reasons for proper installation of industrial cable trays is to ensure electrical safety. Industrial environments often involve complex electrical systems with high power demands and stringent safety requirements. Proper installation of cable trays helps prevent electrical accidents, fires, and equipment failures by:
Providing secure support: Well-installed cable trays securely hold cables in place, preventing them from sagging, coming into contact with other cables or components, or being exposed to mechanical damage.
Ensuring separation and protection: Properly installed cable trays separate power cables from control and communication cables, reducing the risk of accidental contact and potential hazards such as short circuits or ground faults.
Adhering to safety regulations: Industrial cable tray installations must comply with national and international codes, standards, and regulations, such as the National Electric Code (NEC) in the United States. Compliance with these guidelines ensures that cable trays meet the required clearances, support intervals, grounding and bonding practices, and other safety provisions.
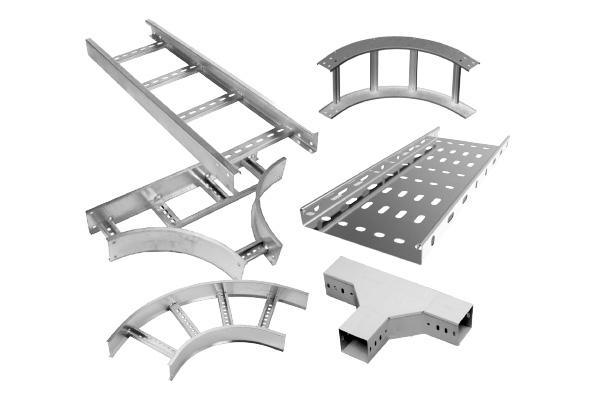
2. Compliance with Regulations and Standards
Proper installation of industrial cable trays is not only important for electrical safety but also for compliance with regulatory requirements. Non-compliant installations can lead to penalties, fines, or legal liabilities, impacting the reputation and financial stability of the facility. Key aspects of compliance include:
Clearances and spacing: Industrial cable trays should be installed with appropriate clearances from combustible materials, structural elements, and other electrical components. Support intervals should also adhere to manufacturer recommendations or industry standards to maintain structural integrity.
Grounding and bonding: Proper grounding and bonding practices are essential for industrial cable trays to ensure safe and effective fault current dissipation. This involves connecting cable trays to the facility’s grounding system using approved methods and materials.
Labeling and documentation: Accurate labeling and documentation of cable trays and their contents facilitate maintenance, repairs, and inspections, helping to identify potential issues before they escalate into more significant problems.
3. System Reliability and Performance
Proper installation of industrial cable trays contributes significantly to the overall reliability and performance of electrical systems. Key factors that influence system performance include:
Cable support and stress reduction: Well-installed cable trays provide adequate support for cables, minimizing stress on connections and reducing the risk of damage due to sagging or vibration. This helps maintain the integrity of cables and extends their lifespan.
Efficient heat dissipation: Proper organization of cables within trays promotes efficient heat dissipation, reducing the risk of overheating and improving the overall energy efficiency of the electrical system.
Reduced signal interference: Separating power cables from control and communication cables within properly installed cable trays minimizes electromagnetic interference, ensuring optimal signal quality and system performance.
4. Cost Efficiency and Resource Optimization
Proper installation of industrial cable trays can lead to cost savings and resource optimization in the long run. Some of the ways in which proper installation contributes to cost efficiency include:
Minimizing repair and replacement costs: By ensuring that cable trays are installed correctly the first time, facilities can avoid expensive repairs, replacements, or downtime caused by faulty installations.
Optimizing tray utilization: Proper installation allows for efficient use of cable trays, reducing the need for additional trays or accessories and minimizing waste.
Facilitating maintenance and upgrades: Well-installed cable trays enable easier maintenance and upgrades, saving time and resources while ensuring minimal disruption to operations.
5. Aesthetics and Workspace Organization
In industrial environments, cable management plays a role in maintaining a clean, organized, and safe workspace. Proper installation of industrial cable trays helps achieve these goals by:
Concealing cables: Installing cable trays above ceilings, below floors, or along walls helps conceal cables, reducing clutter and improving the overall aesthetics of the workspace.
Minimizing trip hazards: Properly installed cable trays keep cables off the floor, reducing the risk of trip hazards and enhancing workplace safety.
Enhancing functionality: Organized cable routing within trays enables easy access for maintenance and upgrades, improving the functionality and productivity of the workspace.
6. Future Expansion and Flexibility
Proper installation of industrial cable trays allows for easy expansion, modification, or reconfiguration of electrical systems as the facility’s needs change over time. Key considerations for future flexibility include:
Adequate planning: During installation, it is essential to consider the facility’s potential growth and evolving electrical requirements. This may involve installing larger or more versatile cable trays,预留 space for additional cables, or incorporating modular designs.
Accessible design: Proper installation should ensure that cable trays are easily accessible for future modifications or additions without compromising safety, efficiency, or structural integrity.
7. Maintenance and Inspection
Installing industrial cable trays according to best practices enables easier maintenance and inspection processes. Key aspects of maintenance and inspection include:
Accessibility: Proper installation should ensure that cable trays are easily accessible for routine inspections, repairs, or upgrades without causing disruptions to operations.
Documentation and labeling: Accurate documentation and labeling of cable trays and their contents facilitate maintenance and inspection processes, helping technicians quickly identify and address potential issues.
Regular inspections: Scheduled inspections of installed cable trays help identify signs of wear, damage, or corrosion, allowing for timely repairs or replacements to maintain system performance and safety.
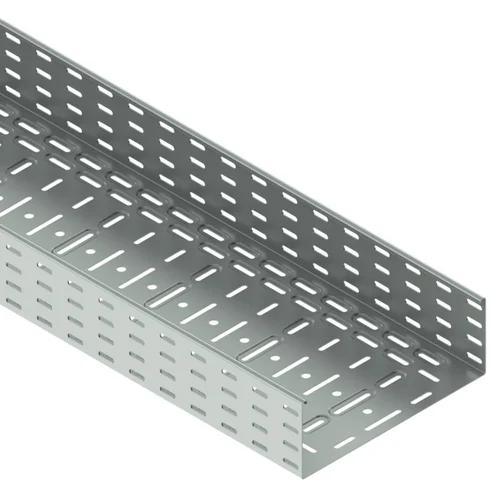
Conclusion
Proper installation of industrial cable trays is vital for ensuring electrical safety, complying with regulations, maintaining system reliability and performance, achieving cost efficiency, enhancing workspace aesthetics and organization, enabling future expansion, and facilitating maintenance and inspection processes. Investing in professional installation services and adhering to industry best practices is crucial for realizing the full benefits of industrial cable trays and optimizing the performance of electrical infrastructure in industrial facilities.
By understanding the importance of proper installation and addressing the various aspects involved in the installation process, facility managers and electrical engineers can make informed decisions that contribute to the long-term success and sustainability of their industrial operations.